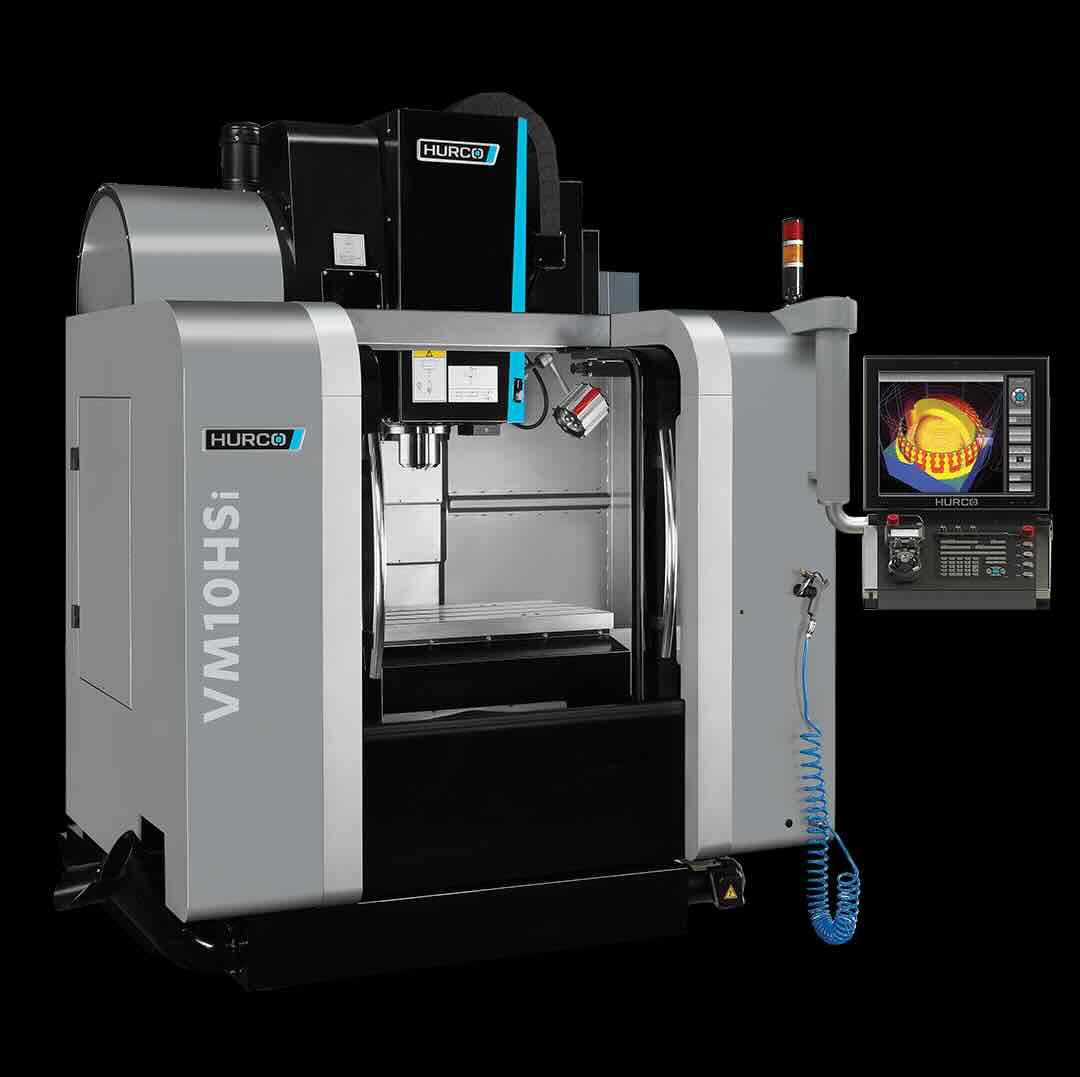
La industria metalmecánica ha experimentado una transformación significativa en las últimas décadas gracias a la incorporación de tecnologías avanzadas, entre las que destacan las máquinas CNC.
Estas herramientas automatizadas se han convertido en elementos esenciales para mejorar la precisión, la eficiencia y la productividad en los procesos de fabricación.
CNC en la producción metalmecánica: usos y ventajas
Las máquinas CNC han revolucionado la forma en que se lleva a cabo la producción en la industria metalmecánica. A continuación, detallamos algunos de los principales beneficios de utilizar estas herramientas avanzadas:
- Mayor precisión y repetibilidad: Una de las principales ventajas de este tipo de máquinas es su capacidad para realizar cortes y trabajos con una precisión milimétrica. A diferencia de las máquinas convencionales, estas permiten programar operaciones complejas con una exactitud constante, lo que reduce el margen de error y asegura una calidad consistente en cada pieza producida.
- Reducción de tiempos de producción: Las máquinas CNC automatizan muchas de las operaciones que, de otro modo, serían realizadas manualmente. Esto permite que las tareas se completen más rápidamente, aumentando la eficiencia en la planta de producción. Además, su velocidad se puede ajustar para optimizar los tiempos de trabajo sin comprometer la calidad.
- Flexibilidad en los procesos de fabricación: Las máquinas CNC son extremadamente versátiles y pueden realizar una amplia variedad de tareas, como torneado, fresado, perforado y corte de metales. Esta flexibilidad permite a los fabricantes adaptarse rápidamente a nuevas demandas del mercado o realizar lotes pequeños de productos personalizados sin la necesidad de cambiar equipos o herramientas constantemente.
- Reducción de costos operativos: Aunque la inversión inicial en una de estas máquinas puede ser alta, el ahorro a largo plazo es significativo puesto que requieren menos intervención manual, lo que reduce los costos laborales y el riesgo de errores humanos. Además, la eficiencia en el uso de materiales y la menor cantidad de desperdicios también contribuyen a la reducción de costos operativos.
- Mejor control de calidad: Las máquinas CNC permiten realizar un seguimiento detallado de cada proceso de producción, lo que facilita la implementación de sistemas de control de calidad más rigurosos. Gracias a la capacidad de programar parámetros específicos, se pueden realizar ajustes en tiempo real para asegurar que cada pieza cumpla con los estándares requeridos.
Casos de éxito y ejemplos en la industria
En los últimos años, numerosas empresas de la industria metalmecánica han adoptado esta tecnología, obteniendo resultados sobresalientes. A continuación, algunos ejemplos:
- Automotriz: La industria automotriz es un claro ejemplo de la adopción exitosa de máquinas CNC. Fabricantes como Toyota y BMW las utilizan para la producción de componentes altamente precisos, como partes del motor y del chasis.
- La automatización de estos procesos no solo ha incrementado la velocidad de producción, sino que también ha mejorado la seguridad y la fiabilidad de los vehículos.
- Aeroespacial: Empresas como Boeing y Airbus emplean máquinas CNC para la fabricación de piezas críticas de aeronaves, como turbinas, fuselajes y alas. Su precisión es esencial en esta industria, donde la mínima variación en las dimensiones de las piezas puede tener consecuencias significativas.
- Fabricación de maquinaria pesada: En la construcción de maquinaria industrial, las máquinas CNC permiten crear piezas de gran tamaño y con una complejidad geometría que sería difícil de lograr con métodos convencionales. Empresas que fabrican prensas, tornos y otros equipos pesados se benefician enormemente de la versatilidad y precisión que ofrecen estas tecnologías.
Cómo elegir la máquina CNC adecuada según las necesidades del negocio
Al elegir una máquina CNC para su negocio, es fundamental considerar varios factores clave:
Estos son algunos aspectos que debe tener en cuenta:
- Mantenimiento y soporte técnico: Asegúrese de que la máquina CNC que elija cuente con buen soporte técnico y opciones de mantenimiento. El tiempo de inactividad por fallas mecánicas o problemas en el software puede afectar gravemente la productividad.
- Tipo de proceso requerido: Dependiendo de las operaciones que se necesiten realizar (fresado, torneado, perforado, etc.), es necesario seleccionar una máquina especializada. Existen máquinas CNC de 3, 4 y 5 ejes, que ofrecen distintos niveles de complejidad y capacidad de trabajo.
- Tamaño de la pieza y capacidad de carga: Es importante seleccionar una CNC máquina con la capacidad de manejar el tamaño y peso de las piezas que se producirán. Esto garantizará la estabilidad y precisión durante las operaciones.
- Software y compatibilidad: Las máquinas CNC dependen de software especializado para la programación. Asegúrese de que el sistema de control de la máquina sea compatible con el software de diseño y modelado que utiliza su empresa (por ejemplo, CAD/CAM).
- Presupuesto y retorno de inversión: Aunque las máquinas CNC pueden ser costosas, es crucial analizar el retorno de inversión a largo plazo. Considere los ahorros en mano de obra, la reducción de desperdicios y los beneficios en cuanto a calidad y productividad al hacer la compra.
Si buscas asesoría para la compra de maquinaria CNC, encuentra la mejor opción en nuestro catálogo o contacta directamente a nuestros asesores.