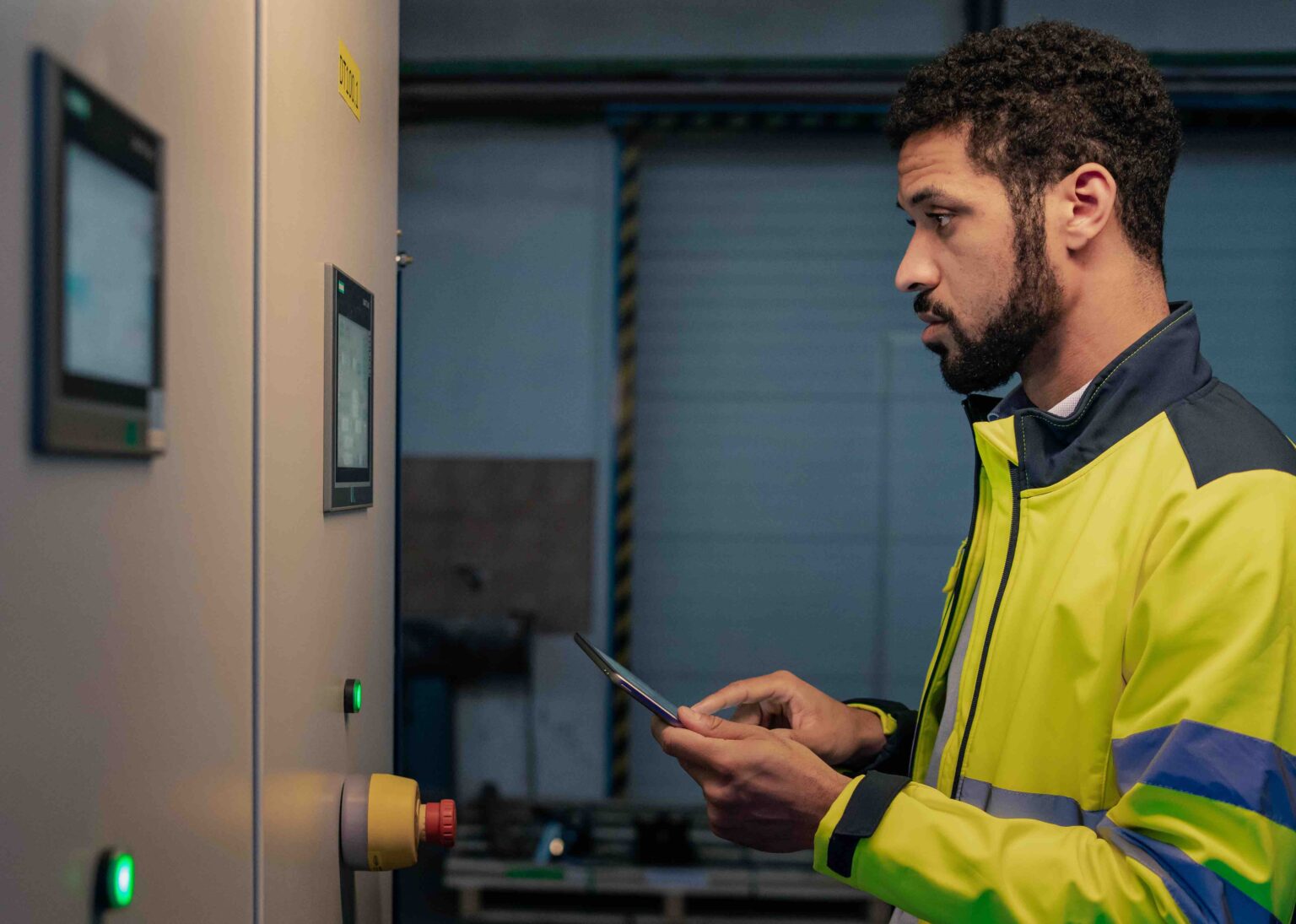
La industria metalmecánica es un sector fundamental para el desarrollo económico global, ya que abarca una variedad de procesos productivos desde la fabricación de maquinaria y equipos, hasta sus componentes y estructuras.
Con la constante evolución tecnológica y los cambios en las demandas del mercado, las innovaciones para 2025 en esta industria marcan un nuevo rumbo hacia la automatización, la eficiencia y la sustentabilidad.
En este artículo, exploraremos las tendencias en metalmecánica clave de la industria, su relación con el sector automotriz, los desafíos geopolíticos y de sustentabilidad.
Asimismo, conoceremos más sobre los nuevos materiales para la fabricación de componentes de vehículos.
Tendencias de la industria metalmecánica en 2025
Las tendencias de metalmecánica para 2025 apuntan hacia la integración de tecnologías avanzadas para mejorar los procesos de manufactura. Entre las principales innovaciones destacan:
1. Digitalización y automatización
La digitalización y la automatización continúan siendo un pilar central en la industria metalmecánica.
El uso de herramientas como la fabricación asistida por computadora (CAM), la inteligencia artificial (IA) y los robots colaborativos (cobots) están revolucionando la producción.
Estas tecnologías permiten a las empresas mejorar la precisión, reducir tiempos de ciclo y minimizar errores humanos.
Esto se traduce en una mayor eficiencia y menores costos operativos.
2. Fabricación aditiva (impresión 3D)
La impresión 3D sigue ganando terreno en la industria metalmecánica debido a su capacidad para producir piezas complejas con gran precisión y menos desperdicio de material.
En 2025, se espera que la adopción de esta tecnología continúe creciendo, permitiendo la fabricación de componentes a medida, especialmente en sectores como la aeronáutica, la automoción y la fabricación de maquinaria industrial.
3. IoT y mantenimiento predictivo
El Internet de las Cosas (IoT) ha llegado para revolucionar la forma en que las empresas gestionan sus equipos.
Los sensores conectados a máquinas permiten monitorear su estado en tiempo real y anticipar fallas antes de que ocurran, lo que optimiza el mantenimiento y reduce los tiempos de inactividad.
En el año 2025, la integración de estas soluciones será más accesible para empresas de todos los tamaños.
Impacto en el sector automotriz
El sector automotriz es uno de los más importantes dentro de la industria metalmecánica, y su evolución está marcada por una fuerte tendencia hacia la electrificación y la movilidad sostenible.
En 2025, veremos las siguientes innovaciones clave:
1. Componentes más livianos
Con el aumento de la demanda de vehículos eléctricos (VE), el sector automotriz está impulsando el uso de materiales más ligeros para reducir el peso de los vehículos y mejorar la eficiencia energética.
Materiales como el aluminio, el magnesio y los plásticos reforzados con fibra de carbono están ganando popularidad en la fabricación de componentes estructurales.
La industria metalmecánica está evolucionando para satisfacer esta necesidad de materiales de alta resistencia y bajo peso.
2. Nuevas tecnologías de fabricación de componentes
Las empresas del sector automotriz están adoptando tecnologías de manufactura avanzadas como el corte por láser, la soldadura por fricción y la estampación de alta velocidad para crear componentes más complejos y resistentes.
Además, la impresión 3D se está utilizando para producir prototipos rápidos y componentes de baja producción.
Desafíos geopolíticos y de sustentabilidad en la industria metalmecánica
La industria metalmecánica enfrenta diversos desafíos geopolíticos y de sustentabilidad que influirán en su desarrollo en los próximos años.
1. Aranceles y políticas comerciales
Los aranceles y las políticas comerciales internacionales continúan siendo un tema crucial para las empresas de la industria metalmecánica, especialmente para aquellas involucradas en la manufactura y exportación de componentes.
Las fluctuaciones en las tarifas arancelarias pueden afectar la rentabilidad de las empresas, lo que obliga a los fabricantes a adaptarse rápidamente a los cambios y a optimizar sus cadenas de suministro.
2. Sustentabilidad y reducción de la huella de carbono
Uno de los desafíos más importantes es la creciente presión por parte de gobiernos y consumidores para adoptar prácticas más sostenibles.
En 2025, se espera que las empresas de la industria metalmecánica aumenten sus esfuerzos para reducir la huella de carbono mediante el uso de energías renovables en sus procesos de producción, el reciclaje de materiales y la optimización del uso de recursos.
Claramente, la transición hacia la sustentabilidad no solo responde a una demanda ética, sino que también se convierte en una ventaja competitiva en el mercado global.
Nuevos materiales para componentes de vehículos
Los nuevos materiales juegan un papel crucial en la innovación de la industria metalmecánica, especialmente en el sector automotriz.
A medida que los fabricantes de automóviles buscan soluciones más eficientes y respetuosas con el medio ambiente, surgen nuevos materiales que mejoran el rendimiento y la sostenibilidad de los vehículos.
1. Materiales compuestos avanzados
Los materiales compuestos, como los plásticos reforzados con fibra de carbono (CFRP) y fibra de vidrio, están siendo utilizados para reducir el peso de los vehículos sin comprometer la resistencia.
Estos materiales son ideales para la fabricación de componentes de vehículos eléctricos, donde la reducción de peso es esencial para maximizar la autonomía de la batería.
2. Acero de alta resistencia
El acero sigue siendo uno de los materiales más utilizados en la industria metalmecánica, y los avances en la tecnología de acero de alta resistencia permiten la producción de componentes más ligeros y duraderos para el sector automotriz.
Así, estos aceros de alta resistencia también ofrecen beneficios en términos de seguridad y desempeño estructural.
En 2025, la industria metalmecánica se encuentra en un punto de inflexión, donde la digitalización, la automatización y la innovación en materiales jugarán un papel crucial para satisfacer las demandas del mercado.
Conoce las tendencias en metalmecánica, súmate a la vanguardia, y conoce el catálogo de máquinas herramienta que puedes integrar a tu empresa.