En la industria metalmecánica, los tratamientos térmicos juegan un papel fundamental en la mejora de las propiedades físicas y mecánicas de los metales de los componentes clave en máquinas industriales.
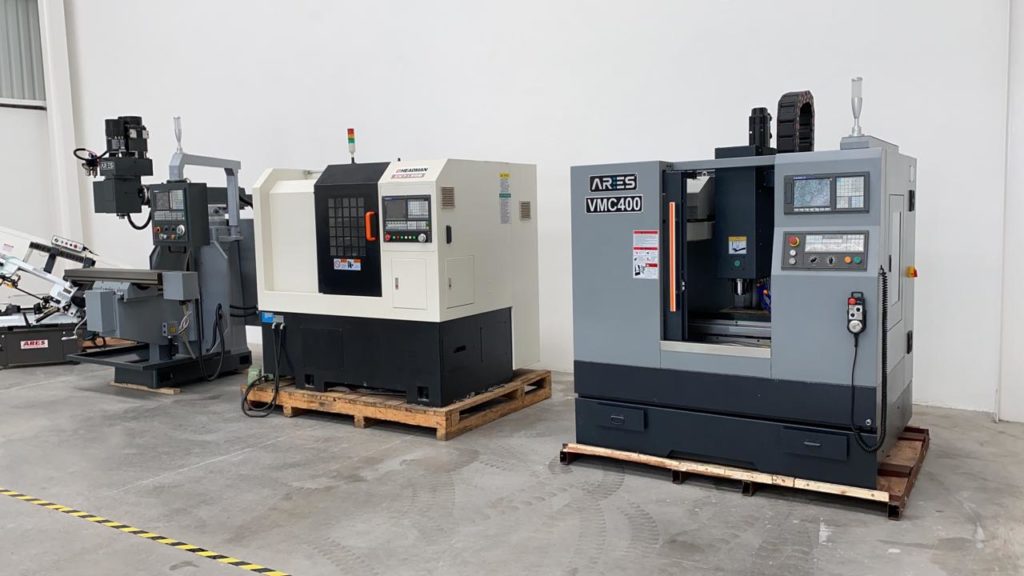
Estos procesos controlados de calentamiento y enfriamiento de los materiales se emplean para optimizar características como la dureza, la tenacidad y la resistencia al desgaste de componentes clave utilizados en montajes de máquinas.
Además, los tratamientos superficiales complementan los tratamientos térmicos, proporcionando una protección adicional a las piezas expuestas a condiciones extremas. Este artículo analiza los diferentes tipos de tratamientos, sus procesos, el equipo especializado utilizado y las medidas de seguridad necesarias en estos procedimientos.
¿Qué son los tratamientos térmicos?
Son procesos industriales que implican el calentamiento y enfriamiento controlado de los materiales, generalmente metales, con el fin de modificar sus propiedades físicas y mecánicas.
Estos tratamientos no alteran la composición química del material, sino que modifican su estructura interna, y son fundamentales para mejorar la resistencia, la dureza, la ductilidad y la tenacidad de los componentes metálicos, garantizando que puedan soportar las demandas del entorno industrial, especialmente en componentes críticos de máquinas industriales.
Los tratamientos térmicos más comunes incluyen procesos como el temple, el recocido, la normalización y la cementación, que se utilizan para cumplir con diferentes objetivos según las necesidades del material y el uso final del componente.
Clasificación y tipos de tratamientos
Los tratamientos superficiales se aplican a la capa exterior de las piezas metálicas para mejorar características como la resistencia al desgaste, la dureza superficial, la protección contra la corrosión y la resistencia a la fatiga. Los tratamientos superficiales incluyen diversos procesos, entre los que destacan:
Nitruración: Implica la introducción de nitrógeno en la superficie del metal, mejorando la dureza y la resistencia a la corrosión. Es ideal para piezas sometidas a alta fricción, como los engranajes.
Cementación: Aumenta la dureza de la superficie de los metales sin afectar su núcleo, lo que es ideal para componentes como ejes, piñones y otras piezas que necesitan resistencia al desgaste en la superficie pero manteniendo la tenacidad interna.
Recubrimientos duros: Se aplican capas metálicas o cerámicas sobre las superficies de los componentes para protegerlos del desgaste y la corrosión. Es común en piezas de alto rendimiento que operan en condiciones extremas, como las partes móviles de máquinas industriales.
Galvanizado: Consiste en recubrir una pieza con una capa de zinc para protegerla contra la corrosión, especialmente en ambientes húmedos o agresivos.
Anodización: Este proceso se utiliza principalmente en aleaciones de aluminio, creando una capa de óxido que mejora la resistencia a la corrosión y proporciona una mayor dureza superficial.
Procesos de los tratamientos térmicos
Los tratamientos térmicos son procesos meticulosamente controlados que incluyen varias etapas esenciales:
Calentamiento: La pieza metálica se calienta a una temperatura específica para alcanzar la microestructura deseada. La temperatura debe ser precisa, ya que un exceso o defecto puede alterar las propiedades del material.
Mantenimiento de temperatura: Una vez alcanzada la temperatura deseada, se mantiene durante un tiempo determinado para permitir que se logren las transformaciones estructurales en el material.
Enfriamiento: El enfriamiento es una de las etapas más críticas del proceso. El tipo de enfriamiento —rápido o lento— depende del tratamiento térmico que se esté realizando. En procesos como el temple, el enfriamiento rápido con agua o aceite aumenta la dureza del material. En otros, como el recocido, el enfriamiento lento reduce las tensiones internas y aumenta la ductilidad.
Equipo especializado para tratamiento de superficies
El tratamiento de superficies requiere de equipos especializados para garantizar que las piezas se sometan a las condiciones óptimas de temperatura, presión y atmósfera controlada. Los equipos más utilizados incluyen:
Hornos industriales: Son esenciales en procesos como el temple, el recocido y la normalización. Los hornos pueden ser de inducción, de convección o de resistencia eléctrica, según el tipo de tratamiento y las especificaciones del material.
Baños de nitruración: Utilizados para el proceso de nitruración, estos equipos permiten la infiltración controlada de nitrógeno en la superficie de las piezas metálicas.
Máquinas de recubrimiento: Estas máquinas aplican recubrimientos duros o galvanizados en la superficie de las piezas metálicas. Se pueden utilizar técnicas como la pulverización térmica o el baño de inmersión para asegurar una capa uniforme y adherente.
Equipos de soldadura: En algunos tratamientos superficiales, como la soldadura de recubrimientos, se requiere de equipos específicos para aplicar capas metálicas sobre el sustrato base.
Medidas de seguridad en los tratamientos térmicos
Los tratamientos térmicos y tratamientos superficiales involucran procesos que pueden ser peligrosos si no se toman las precauciones adecuadas.
Las altas temperaturas, las sustancias químicas y los procesos de presión requieren estrictas medidas de seguridad, tales como el uso de ropa y máscaras adecuadas para la protección personal, el monitoreo de temperatura de los hornos y de los niveles de gases, ventilación adecuada y mantenimiento de los equipos industriales.
Por lo tanto, la correcta aplicación de estos tratamientos depende de un adecuado control de procesos, el uso de máquinas industriales especializadas y el cumplimiento de estrictas medidas de seguridad.
Los avances en estas tecnologías continúan permitiendo que las máquinas industriales y los montajes de máquinas sean más eficientes, duraderos y capaces de soportar las exigencias del entorno industrial moderno.
Contacta a los asesores de Tecnomaquinaria para obtener más información sobre el mantenimiento de tu equipo y las opciones que existen para tu maquinaria.