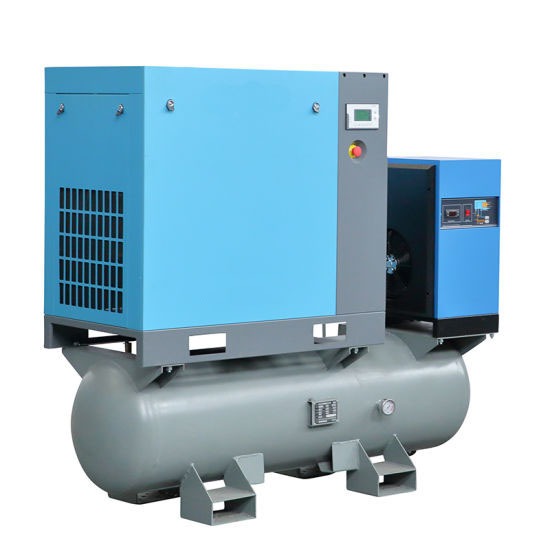
El compresor industrial de aire es una pieza clave en múltiples sectores productivos, desde la industria metalmecánica hasta la alimentaria. A pesar de su relevancia, muchos talleres y fábricas operan estos equipos sin estrategias claras de eficiencia, lo que genera altos costos de energía, fallas prematuras y tiempos muertos.
Optimizar el uso del aire comprimido no solo prolonga la vida útil del compresor, sino que también representa una oportunidad real para mejorar la eficiencia energética en compresores, reducir el gasto eléctrico y contribuir a la sostenibilidad de la planta.
En este artículo analizaremos los principales factores que afectan el rendimiento de un compresor, consejos de mantenimiento preventivo y cómo los sensores inteligentes pueden transformar el consumo energético en la industria.
Factores que afectan el rendimiento de un compresor industrial
El rendimiento de un compresor de aire industrial depende de múltiples variables, muchas de las cuales pueden ser gestionadas para evitar pérdidas de energía y sobrecargas innecesarias.
1. Tamaño y capacidad del compresor
Utilizar un compresor sobredimensionado genera consumos energéticos innecesarios, mientras que uno subdimensionado trabaja al límite de su capacidad, lo que provoca desgaste acelerado y menor vida útil. Por ello, es vital seleccionar un equipo que se ajuste al perfil de demanda de aire comprimido en tu línea de producción.
2. Condiciones ambientales
El aire caliente, húmedo o con partículas contaminantes puede reducir significativamente el rendimiento. Temperaturas elevadas en el cuarto del compresor, mala ventilación o presencia de polvo afectan la eficiencia del sistema y aceleran el desgaste de componentes internos.
3. Fugas en la red de aire comprimido
Uno de los principales enemigos de la eficiencia energética en compresores son las fugas; una red sin mantenimiento puede perder entre el 20% y 30% del aire producido, lo que implica mayor tiempo de operación y consumo de energía innecesario.
4. Configuración del sistema
La presión de trabajo influye directamente en el consumo energético: por cada bar de presión adicional, el consumo eléctrico puede aumentar entre 6% y 10%. Mantener la presión dentro del rango óptimo, sin excesos, es clave para ahorrar energía.
Consejos de mantenimiento para evitar sobrecargas
El mantenimiento de compresores es esencial no solo para garantizar su funcionamiento continuo, sino también para evitar picos de consumo eléctrico y paros por fallas inesperadas.
1. Revisión y cambio de filtros
Los filtros de aire, aceite y separadores deben inspeccionarse regularmente. Filtros obstruidos obligan al compresor a trabajar con más esfuerzo, aumentando el consumo energético y reduciendo el caudal disponible de aire.
Consejo: Establece una rutina de revisión semanal y sigue las recomendaciones del fabricante para el cambio de filtros.
2. Control del nivel de aceite
En compresores lubricados, el nivel y estado del aceite influye en la eficiencia del sistema. El aceite degradado o escaso genera mayor fricción, calor y esfuerzo para el motor.
Consejo: Utiliza aceite de calidad y cambia el lubricante según las horas de trabajo del compresor.
3. Limpieza del sistema de refrigeración
El sobrecalentamiento es una de las causas más comunes de fallo. Una mala disipación del calor puede deberse a obstrucciones en el radiador, acumulación de suciedad o fallas en los ventiladores.
Consejo: Limpia el radiador con aire a presión regularmente y asegúrate de que el flujo de aire de ventilación no esté bloqueado.
4. Drenaje automático de condensados
La humedad contenida en el aire se convierte en agua dentro del sistema. Si no se elimina adecuadamente, puede dañar componentes internos y reducir la eficiencia del compresor.
Consejo: Instala purgadores automáticos en el tanque y en puntos bajos del sistema para evitar acumulación de agua.
Consumo energético y ahorro con sensores inteligentes
La tecnología actual permite llevar el control del aire comprimido en la industria a un nuevo nivel mediante sistemas de monitoreo y automatización con sensores inteligentes.
¿Cómo ayudan los sensores a mejorar la eficiencia energética?
- Monitoreo en tiempo real: Los sensores permiten visualizar el consumo de energía, presión y caudal de aire, identificando patrones ineficientes o puntos críticos.
- Detección automática de fugas: Equipos con sensores de flujo y presión detectan pérdidas mínimas en la red, lo que facilita su reparación oportuna.
- Ajuste dinámico de carga: Los sensores pueden regular la operación del compresor según la demanda, evitando ciclos de trabajo innecesarios o sobrecargas.
- Mantenimiento predictivo: Gracias a la recopilación de datos, los sensores ayudan a anticipar fallos mecánicos, permitiendo programar mantenimientos antes de que ocurran paros inesperados.
Inversión con retorno garantizado
Si bien la instalación de sensores o la actualización del sistema puede requerir una inversión inicial, los ahorros energéticos obtenidos a lo largo del tiempo permiten recuperar el costo rápidamente. De hecho, implementar un sistema de monitoreo puede reducir hasta un 30% el consumo de energía en sistemas de aire comprimido industriales.
Buenas prácticas para una operación eficiente
Además del mantenimiento y la tecnología, implementar una cultura de uso eficiente del aire comprimido es fundamental para lograr resultados sostenibles:
- Capacita al personal: Asegúrate de que los operadores comprendan cómo usar el compresor de forma eficiente y detectar señales de falla.
- Apaga el compresor fuera de turnos: Un compresor encendido sin carga sigue consumiendo energía. Automatiza su apagado durante periodos de inactividad.
- Utiliza aire comprimido solo cuando sea necesario: Muchos procesos pueden sustituirse con sistemas eléctricos o mecánicos más eficientes.
El compresor de aire industrial es uno de los equipos más demandantes en términos de energía dentro de una planta. Sin embargo, con un mantenimiento adecuado, control de fugas, monitoreo en tiempo real y el uso de sensores inteligentes, es posible convertirlo en un aliado de la eficiencia energética en compresores.
Optimizar el sistema de aire comprimido en la industria no solo reduce los costos operativos, sino que también mejora la confiabilidad de la producción, prolonga la vida útil del equipo y contribuye a las metas de sostenibilidad.
Si estás evaluando una renovación de tu sistema o buscas mejorar el rendimiento de tu equipo actual, recuerda que pequeñas acciones bien dirigidas pueden generar grandes ahorros a largo plazo.
En Tecnomaquinaria tenemos venta de maquinaria industrial, y una amplia gama de máquinas y herramientas para tu taller. Encuentra la tuya en nuestro catálogo y contáctanos para más información.